The performance of an industrial wastewater treatment plant depends largely on the accuracy and technical prowess with which it is managed. This is the reason why Saur Industrie works on the basis of full transparency and clear communication, focusing on people rather than technical issues; a strategy that is paying off impressively for this juice and soft drinks production unit.
The necessity of treating industrial wastewater
In today’s world, treating industrial wastewater is a non-negotiable necessity, not only in terms of regulatory compliance, but also of corporate image and environmental responsibility. This is particularly true for drinks producers. Since water is their main raw material, these companies pay particularly close attention to its quality, especially since their effluents tend to be irregular in terms of flow, composition and pollutant concentration. This fact introduces an additional level of complexity for those who operate this kind of treatment plant.
For example, the industrial wastewater treatment plant serving this production site pre-treats its inflows before discharging them to be further treated in the local authority facilities. Nevertheless, the production plant managers were struggling to stay below the quantity and quality thresholds set out in a discharge agreement. So the decision to work with Saur Industrie was driven essentially by the desire to achieve greater transparency.

A more detailed understanding of the treatment system
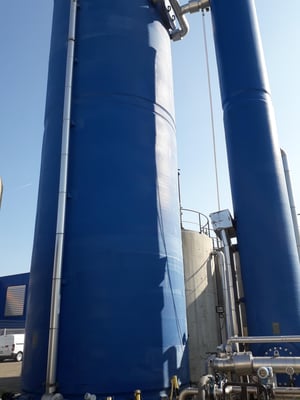
Previously, this industrial wastewater treatment plant was operated in a less proactive way with very little interactive communication between the treatment plant and production teams. It was seen as a simple system in place purely to receive the effluents produced by the plant, with no effective post-analysis corrections being applied. The manufacturer lacked the experience of feedback and, at an even more basic level, had a very poor understanding of its wastewater treatment system.
So Saur Industrie provided basic training to introduce all site production teams to the key operating principles of the treatment plant located at the entrance to their place of work. This provided them with a better understanding of why this system represents a cost to their employer, and highlighted the impact that day-to-day actions can have not only on treatment plant operation, but also on the image of their production plant.
This program was designed to build a close and open relationship between the treatment plant operator and the company, opening the door to faster identification of pollution, and the flexibility required to adapt treatments to conditions. Performance can only be achieved if the manufacturer and operator target the same goals in terms of transparency and continuous optimization.
A wastewater treatment plant that is now central to production
Saur Industrie also committed itself to gaining a detailed understanding of the production process and its associated effluents. Such initiatives can succeed only where there is active and constructive collaboration with on-site managers (Environment, QSE, Senior Management, Maintenance, Utilities, etc.) with the shared aim of anticipating and improving industrial wastewater treatment plant performance. The first step was to identify the pollutants discharged by the production plant.
In the case of this soft drinks manufacturer, that proved to be mainly sugar. The next stage was to implement a specific monitoring system to identify which indicator best highlighted raw material losses and the types of pollution likely to arrive as inflows to the industrial wastewater treatment plant.
Measuring the organic pollution content - and particularly sugar - contained in the water flowing into the treatment plant, and then recording those values continuously together with the associated alarms made it possible for all those involved to:
- manage the plant more efficiently
- assess the incoming pollution more accurately, and therefore manage it more appropriately
The result has been higher rates of compliance with the terms of the discharge agreement.
Feeding that information back to the production teams in real time has also boosted production performance levels.
This new and more proactive method of industrial wastewater treatment plant management is also delivering clearly identifiable cost savings. In the past, the site used an external service provider to process some of its waste. Today’s better understanding of the variations in inflow loads entering the treatment plant has enabled this waste to be reintroduced into the internal treatment circuit at times where additional load is permissible. None of these improvements and enhancements have had any negative financial effect. They have also enabled the methanization unit to use the biogas much more effectively to fuel a boiler. So the amount of biogas flared off has been halved by using it to fuel the hot water boiler to heat the effluent.
Want to know more?
Take a look at our eBook guide on this subject or e-mail us at: saur.industrie@saur.com
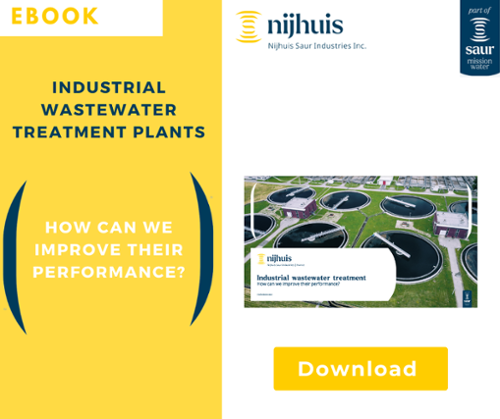