The pressure on water resources is increasing incrementally day by day. For industrial users, this has become a critical issue. That’s because no water = no production. So whether that water is sourced from the public supply system or abstracted from a river or borehole, this is a very closely monitored challenge.
- So what questions should you be asking yourself about sourcing water from a borehole?
- The need for borehole regeneration
For industrial users, water is now one of the most closely monitored - and most important - process inputs. From water as an ingredient — in the broadest sense of the word — to water for washing, water as a vector for energy, and technical water, this is a precious resource by definition. Apart from the cost burden it places on industrial users, water also - and perhaps more importantly - influences product quality and health safety. Substandard water can result in production line shutdowns, or worse still, product recalls, both of which can have a catastrophic effect on company image.
To ensure guaranteed continuity of supply, industrial users have three options: connection to the public supply system or abstracting water from a borehole or river. This third option is clearly open only to industrial plants located on the banks of fast-flowing rivers, and is subject to prefectoral authorizations. Even then, there may be supply issues, especially in the summer months, when a storage solution may be required. This solution also has the disadvantage of exposing industrial users to the presence of algae or undesirable molecules from upstream (hydrocarbons, pesticides, etc.). River water can also be too hot at some times of the year (drinking water should not exceed 25°C); a new problem that has arisen as a result of global warming.
Connection to the public supply system provides a consistent and quality-compliant source of water, and would appear to be the simplest solution to implement. Nevertheless, industrial users are still advised to make provision for water storage tanks to protect against supply system failures or outages. And it is not the most economical solution.
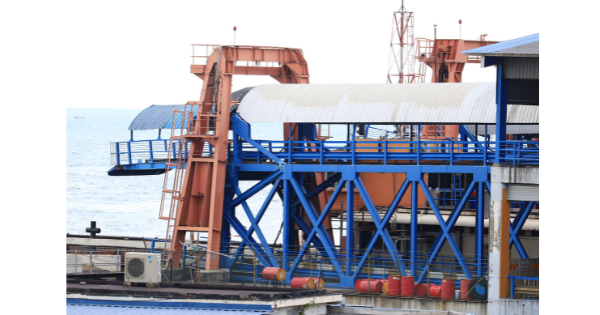
1 - What questions should you be asking yourself about sourcing water from a borehole?
Averaging around €150,000 per unit, the upfront investment may seem high, but drilling boreholes remains the least expensive water supply solution for industrial plants over the long term. Unlike a public supply system connection, using boreholes gives the user complete control over maintenance. Compared with river water abstraction, boreholes have the significant advantage of removing the risks associated with low water flows and surface temperature variations. At between 100 and 150 meters depth, water is constantly between 10 and 12°C, and can therefore be used to provide a direct feed for cooling systems.
Before actioning the borehole option, you should begin by ensuring that the water table has sufficient supplies of groundwater. This is particularly important in some regions where restrictions are sometimes imposed by the authorities. You will also need to install the units and technologies required to treat the water you abstract from the borehole (oxidation towers, filtration and/or disinfection systems, etc.). In most cases, storage tanks are added to the installation to prevent any poor quality water reaching the process. So sourcing your water from a borehole requires a more accurate level of monitoring than a public supply system connection.
This can be mitigated by using publicly available data about local pollution levels and distribution, and innovative tools to monitor the quantity and quality of water abstracted from the borehole. These are particularly important, because boreholes can drift and wear out over time. Water resource quantity measurement solutions are now available to forecast near-term water table levels and compare the actual borehole flow rate against its nominal flow rate; a very efficient way of planning maintenance needs.
2 - The need for borehole regeneration
Water with high fine particle content (erosion residues, soil, vegetation, etc.), a pump failure as a result of mud or sludge or a hydraulic system sized as a result of exposure to water rich in iron or manganese... boreholes are also subject to the ravages of time.
Fortunately though, boreholes can be regenerated: hydraulic system components can simply be extracted from the borehole for deep cleaning, although this can be a difficult and costly task. From a more preventive perspective, the slots in the casing pipes that carry water to the bottom of the borehole can be brushed clean. The bottom of the borehole can also be cleaned using compressed air to remove accumulated mud and sludge. Some operators are even beginning to use ultrasound shock waves for this purpose. Chemical treatments are also an option, but for obvious environmental reasons, their use is declining among industrial users. But whatever method is adopted, it can only really be optimized by using appropriate monitoring systems.
If you have questions about any of these issues, or would welcome expert advice on borehole abstraction as a source of water for your industry... Please contact us to tell us about your project: we can then work with you to identify an appropriate solution.
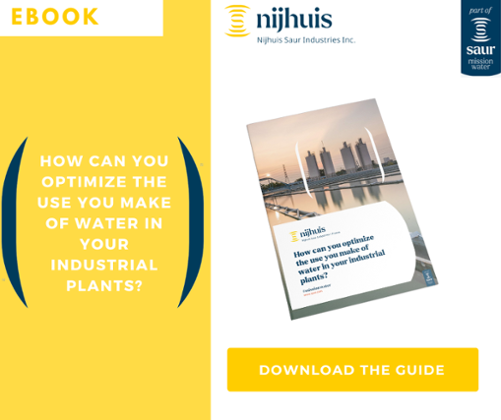